A
Visit To The Snell Memorial Foundation |
by Marcus
Miller
Associate Editor
Beginner Bikes Magazine
On a
beautiful Saturday morning, a group of riders set out from various
parts of the San Francisco Bay Area and rode to the outskirts of
Sacramento to visit the Snell Memorial Foundation. Most of us have
heard of Snell before and some look for the sticker on their helmet
before buying it. We decided to take a tour of the facilities and
see firsthand what helmet testing was all about!
Most states that require helmets mandate DOT (Department
of Transportation) standards. These standards are published by
the U.S. federal government and have been around since 1970. Snell
is an independent non-profit organization that has been testing
helmets since 1959. Unlike DOT, the Snell standard is not mandatory.
Helmet manufacturers may choose to submit helmets to Snell for
testing - if they pass, they get to put a Snell certification
label on their helmet.
A
brief history of Snell: William Pete Snell was an avid amateur
automobile road racer. He
competed in many events and at one SCCA sanctioned race in 1956,
he was involved in a single vehicle rollover accident. Doctors
determined that the accident was survivable in all other ways,
but William died as a result of the head injuries he sustained.
He was wearing a Cromwell helmet; one of the better ones available
in those days. But the cork, fiberboard and leather construction
were simply insufficient to protect him. Dr. George Snivley was
a friend of the family and also an avid car racer. He undertook
what became a life-long project to study helmets and attempt to
quantify their performance through scientific testing.
Our
tour guides for the morning were Ed Becker (Executive Director,
on left), Hung Zhang (Director of Education, on right) and Allen
Harris (Testing Technician, center).
Ed gave us a brief synopsis of why and how the
Snell Memorial Foundation came into existence and then talked
a bit about the standards. What is important to the survivability
of an accident is to limit the force applied to the brain if there
is an impact. A Wayne State University study provided some measurements
based on cadaver brains that suggested that the onset of brain
damage might occur around 400 Gs and forces in excess of 600Gs
would likely result in a fatality. Likewise, a study that compared
helmeted and un-helmeted riders in accidents where both victims
were riding the same motorcycle (driver and passenger - one with
helmet and one without) from 1972-1987 concluded that riders were
2 times more likely to survive if wearing a helmet. The scientists
noted that the odds of survival increasing dramatically towards
the end of the experiment. They attributed this improved survivability
to the improved performance of more modern helmets!
[Finding
the amount of force necessary to bring on brain bramage is problematic.
Wayne State U. smacked corpses in the head and then dissected
the brains looking for visible physical evidence of damage.
Mr. Becker pointed out that you couldn't tell if a corpse suffered
more subtle forms of brain damage like slurred speech or memory
loss. Testing on live animals might uncover useful information
but (ethical treatment of animals questions not withstanding)
the question couldn't be answered just how much the information
derived from a chimp's skull and brain was applicable to human
physiology. - Motorradneuling]
Let the Helmet Bashing
begin!
OK,
this is what we all came for - to watch helmets get bashed, mashed,
crunched and otherwise tested to completion! A copy of the Snell
M2000 standard can be found at http://www.smf.org/pdf/m2000std.pdf
First, the helmet is marked for the areas where
impacts can be administered - this corresponds roughly to the
top half of the head with somewhat lower being allowed in the
back. Allen is shown here using a computerized jig to mark out
the helmet. He also measures visual range at this time - all helmets
must have 105 degrees of lateral visibility both left and right
as well as 7 degrees up and 35 degrees down from horizontal. This
ensures that the helmet will not interfere with the peripheral
vision of the wearer.
Chin
Bar Deflection Test |
Chin Bar Deflection Test: This
was the first test we saw demonstrated. A helmet was strapped
into the test unit and a 5 kg weight (11 lbs) was dropped on the
chin bar. The chin bar must deflect no more than 60 mm from an
impact of 3.5 m/sec. The helmet did just fine and we were quickly
on our way to the next test.
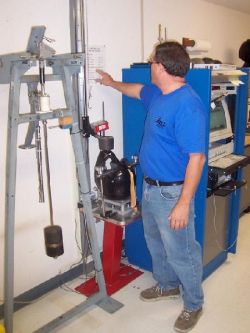
Chin
Bar Deflection Test
Dynamic
Test Of Retention System |
Dynamic Test of Retention System:
After strapping the helmet on the headform, the chinstrap is "pre-stretched"
with a weight and then a second weight is dropped to administer
a quick, sharp blow to the chinstrap.
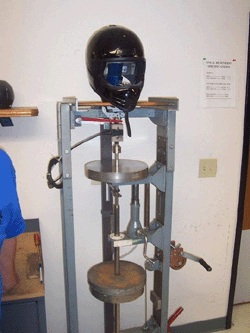
Dynamic Test
of Retention System
The strap must not come undone, break or stretch
by more than 30 mm. Our test helmet showed a deflection of 32
mm - it failed the test!
[We
don't know the manufacturer of this helmet and were asked not
to reveal it even if we recognized it. It was also pointed out
that this helmet was of a model still under development. The
manufacturer will be given the chance to redesign the helmet
and resubmit it for testing before it finds its way onto store
shelves. - Motoradneuling]
Positional
Stability Test |
Positional Stability (Roll-off) Test:
Next, a helmet was fastened to another headform and suspended
so that a weight on the end of a strap could administer a sharp
blow to see if the helmet would get pulled off the headform. A
helmet won't do you any good if it comes off during an accident!
Good news, this helmet passed this test!
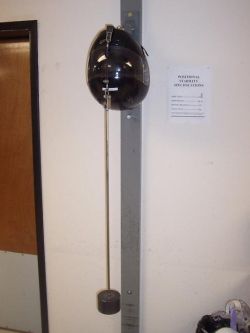
Positional
Stability Test
Impact
Management Test |
Impact Management Tests: This is the one everyone
wanted to see. This is how Snell measures just how much force
your brain might be subjected to in the event of a fall.
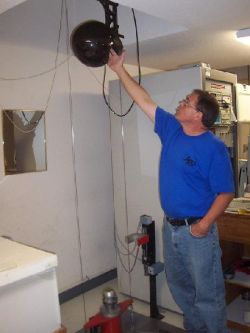
Impact
Management Test Setup
A
headform that approximates the correct shape and weight of a user's
head (there are small, medium, large and extra-large headforms
for the different size helmets) is strapped inside the helmet
along with an accelerometer. To achieve various impact energies,
the apparatus is raised up 3 meters for a 150 joule impact. Push
the button and watch the helmet fall!
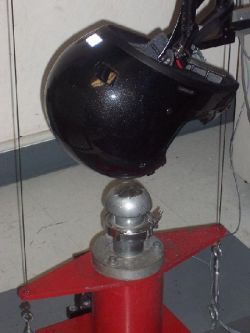
Impact Management
Test One
Whack!
(Everyone cringes - that just doesn't sound good!)
And
then we all peer over at the computer screen - the trace shows
just how many Gs the headform experienced - well under 300Gs!
The helmet did its job - at least the first time. But now Snell
drops it again, this time from 2.2 meters for a 110 joule impact.
Back up goes the helmet and then it comes crashing down again!
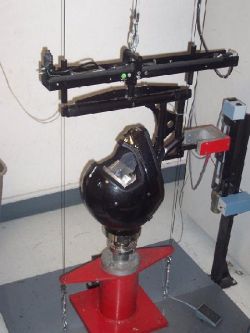
Impact Management
Test Two
Thud!
This
time it's not so painful but its still a terrible sound. Looking
at the graph on the computer screen, we can see that the helmet
has definitely been compromised, but amazingly enough, it still
manages to do its job and keep forces below the 300G level!
We
drop the helmet a few more times on to different shaped anvils:
there's a flat, a hemispherical and even an edge anvil. Our poor
helmet is looking battered and bruised - but surprisingly in some
areas that were impacted you can't see much external damage. The
paint is only slightly blotchy and there is no scratching or chips
of paint missing. This just goes to prove that its difficult to
assess if (and how much) a helmet has been damaged.
One
question that Ed was asked that seems worth bringing up at this
juncture was: "What if a helmet falls out of your hands and
hits the ground? Your head wasn't inside... is the helmet damaged
and need to be replaced?" His answer was that its never a
good idea to let your helmet hit the ground. But, if your head
was not inside, then there is not much weight and thus very little
force for the helmet to dissipate. Most likely, the helmet is
fine - just be careful and don't let it happen again. If you bounce
your helmet on the ground like you're dribbling a basketball,
then all bets are off!
[return
to the top]
Shell
Penetration Test |
Shell Penetration Test: This test, by far, looked
the worst. A 3 kg (6.6lb) SHARPENED striker was raised up 3 meters
above the helmet. Inside the helmet, a piece of paper was placed
between the headform and the helmet - if the striker so much as
even touches the paper, the helmet fails the test.
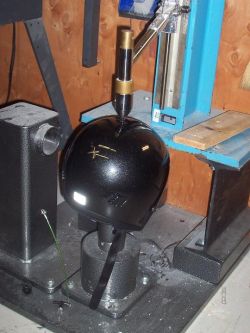
Shell Penetration
Test
Click
- Whoosh - SMACK!
And
down came the striker on to the helmet. It made quite a nice hole
in the outside of the helmet and we held our breath as the helmet
was removed - but when the paper was pulled out of the helmet,
we could all see it hadn't been touched. Amazing!
[return
to the top]
Face
Shield Penetration Test |
Face Shield Penetration Test: This was the last
test we saw demonstrated, and this one also looked unfair to the
helmet. The face shield must survive three strikes from a gun
firing a lead pellet.
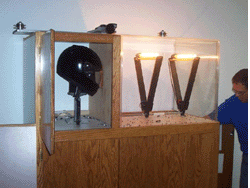
Face Shield
Penetration Test
Allen
pumped up the gun, took aim and shot. Bang - zing - hey, ouch!
Even though all safety precautions are taken, testing can be a
dangerous thing. Just ask Gerald (Motoradneuling). In a freak
occurrence (the first time, according to Allen), the bullet bounced
straight back off the face shield and ricocheted off Allen's ear
and hit Gerald in the cheek. Didn't hurt anyone, but certainly
caught those two by surprise. Good thing we were all wearing our
safety glasses as required! Perhaps we should be wearing our helmets
and all of our safety gear? Hmmm.... The face shield survived
this last test and passed without a problem. No bullet is allowed
to penetrate the visor or else the helmet fails.
[As
Darwin mentioned both Allen and I were both fine but I think
Allen got the worst of the deal. By the time the pellet hit
me it had all the force of a wadded up bubble gum wrapper but
the experience was memorable never the less. I still have the
pellet as a souvenir of my "war wound". - Motorradneuling]
[return
to the top]
Removability
Test |
Removability Test: This final
remaining test wasn't demonstrated; however, armed with only a
pair of shears, simple-edged tools and a flat blade screwdriver,
a technician must be able to remove a helmet that is fastened
on a headform. The trick is, they can't use the buckle or any
other helmet mechanism. The operation must be able to be completed
in less than 30 seconds - this ensures that a helmet can be removed
from an accident victim easily even if the retention system cannot
be operated.
[Darn,
I didn't know about this test or I'd have asked to see it demonstrated.
We could have given tour participants the tools and made a race
out of it. Oh well, now we have an idea for next time. Next
year everybody bring your own Leatherman (the pocket tool, not
the village person). - Motorradneuling]
[return
to the top]
Summary |
All
in all, a very interesting tour! So just how does a manufacturer
get a helmet certified and just how much does Snell make on testing?
The first step is to submit 5 samples for certification testing.
Snell charges $940 and tests 4 of the helmets (one is kept as
an "archive" sample). If there are any failures, then
it's back to the drawing board for the manufacturer.
Once the helmet passes certification, the manufacturer
can label their helmets with a Snell sticker as long as they comply
with continued random sample testing. Each year, Snell goes out
and buys sample helmets from random dealers. Snell charges $120
per helmet (in addition to being reimbursed for purchase price)
to test these helmets. They are subjected to all of the same certification
tests, however testing is done to 90% of the original standards.
If a helmet fails any of the tests, three more samples are bought
and tested. If any of those three fail in the same way as the
first, then the certification can be pulled for the helmet.
[Failures
of production helmets of a certified model often come from quality
control issues during manufacturing. For example, small differences
in temperature and humidity during the drying of the polystyrene
can drastically compromise its shock absorbing properties. -
Motorradneuling]
Certification labels have serial numbers and so
each helmet gets a unique label. The labels are sold to the manufacturer
for 60 cents each. Snell does receive some donations from private
individuals and also applies for some government grants.
What did we learn? Snell takes their testing seriously.
The tests are both sophisticated and at the same time simple.
Is there room for improvement in the world of helmet technology?
Ed stressed that he thought more lives could be saved if helmets
could be made to protect the wearer better.
After our tour, we all went to a local restaurant
and had a great lunch and got to chat some about what we had heard
and seen. We wish to thank Snell for their hospitality and especially
those who took time out of their weekend to come in and show us
what they do at this unique place. It was a very interesting,
informative and educational visit!
[Thanks
also go to Darwin for helping me organize the event and to all
of the participants who made it a success including BeginnerBikes.com
members BandMan (Stephen) and Mark. - Motorradneuling]
[return
to the top] |